Większość detali powstających w procesach drukowania 3D wymaga pewnego poziomu wykończenia powierzchni. Jest to bezpośrednio powiązane z wymaganiami technicznymi na etapie odbioru końcowego części produkcyjnych czy prototypów. Czy mamy do czynienia z drukiem metalu czy tworzyw sztucznych, techniki obróbki wykańczającej są zwykle podobne. Niejednokrotnie za ich udziałem otrzymywane produkty zyskują odpowiedni wygląd, chropowatość powierzchni czy też właściwości mechaniczne. Poprawieniu ulega również proces ewentualnej późniejszej koloryzacji. W zależności od sposobu powstawania wymagane są różne etapy przygotowania powierzchni dla kolejnych obróbek przy wykorzystaniu dedykowanych technologii.
Ważnym punktem wyjścia jest sposób wytwarzania detali, bo w zależności od tego czy pracujemy z detalami po SLS, SLA, FDM czy DMLS, każde z nich posiada inną powierzchnię wyjściową. W przypadku FDM powierzchnia wyjściowa do dalszych etapów uwidacznia ślady łączenia kolejnych warstw, w przypadku SLA powierzchnia jest zdecydowania ładniejsza (słabo widoczne ślady kolejnych warstw) i zapewnia stosunkowo dobry punkt startowy, z kolei elementy po SLS mają dość chropowatą powierzchnię ale już bez widocznych śladów warstwowania, DMLS daje jednorodną powierzchnię o podobnej do SLS chropowatości.
W przypadku wysokiej chropowatości początkowej, należy zmniejszyć jej wartość tak mocno na ile to możliwe. W przypadku detali drukowanych w proszku koniecznym jest pozbycie się go z większości dostępnych miejsc w szybki i efektywny sposób Do tych czynności stosuje się piaskarki kabinowe z opcjami dedykowanymi do tego typu zadań (np. obecność jonizacji, certyfikat ATEX dla wybuchowości, obrotowe kosze, cyklony, systemy kilku dysz). Tego typu kabiny pozwalają na obróbki wielu małych elementów np. w koszu, pojedynczych elementów ręcznie, czy też na pasie transmisyjnym w cyklu automatycznym. Odpowiedni dobór takiej kabiny wynika głównie z takich parametrów jak:
- wielość detali
- ilość detali
- oczekiwany efekt
- zakładana wydajność
- dostępność operatora
- materiał wykonania
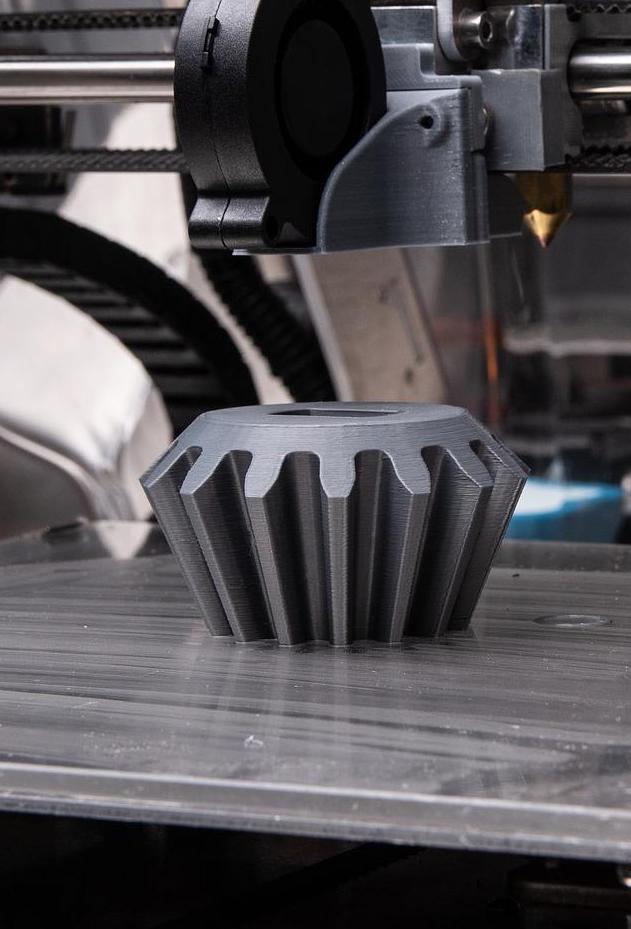
Innym sprawdzonym sposobem masowej obróbki detali po druku 3D jest technologia obróbki wibrościernej lub rotościernej. I podobnie jak w przypadku piaskarek, istotnym z punku widzenia procesu jest doprecyzowanie wymagań dla zadania obróbczego. Dlatego oprócz wielkości detali, ich ilości, itp. ważnym parametrem jest docelowa chropowatość Ra, która po standardowym procesie obróbki pojemnikowej może wynieść ok. 2,5-0,8um, a która w przypadku detali po druku 3D może na starcie wahać w się w granicach zwykle 3-50um w zależności od technologii (w skrajnych przypadkach nawet i 200um). W przypadku dużych wartości obróbka śrutownicza zwykle jest w stanie obniżyć tę wartość o połowę, więc do procesu wibrowania, trafiają detale np. o chropowatości 6-20um. W przypadku obróbki wibracyjnej materiałem obróbczym są kształtki żywiczne, tworzywowe, porcelanowe. Zatem aby dobrać odpowiedni proces potrzebne jest ustalenie jego celu. Do wykonania takiego zadania można wykorzystać maszynę zarówno kołową, korytową jak też szybkoobrotową (która mimo iż wymaga większego nakładu inwestycyjnego to pozwala znacząco skrócić czas procesu). W przypadku obróbki pojemnikowej stosuje się także odpowiednią chemię wspomagającą taki proces. Zaletą wspomnianego procesu jest powtarzalna i jednorodna obróbka wykańczająca.
Uzupełnieniem technologii obróbki wibrościernej jest stosunkowo droga ale szybka, dająca niskie wartości chropowatości końcowej nawet 0,01um i poniżej technologia DLyte. Zwykle stosuje się ją w przypadku bardzo kosztowych elementów, gdzie celem jest uzyskanie np. odpornych korozyjnie, o poprawionych własnościach zmęczeniowych, bez utraty geometrii detali. Oczywiście wymagane jest zwykle pewne, wstępne przygotowanie powierzchni do procesu elektropolerowania.
W przypadku bardzo krytycznych elementów jakimi są np. części lotnicze wykorzystuje się dokładne i powtarzalne systemy zrobotyzowane np. AV&R. Urządzenia wykorzystują szereg różnych narzędzi i odpowiednie oprogramowanie które czuwa na przebiegiem procesu. Takie cele posiadają na wyposażeniu systemy pomiarowe, detekcji, a nawet inspekcji wizualnej co zapewnia otrzymywanie detali o właściwych parametrach końcowych (kształt, wymiary, promienie, chropowatość). Procesy ponadto mogą być prowadzone w sposób adaptacyjny, wychwytując wszelkie odchyłki na detalu, na wejściu.
Oczywiście są sytuacje takie, gdzie nie jest wymagana masowa obróbka detali 3d i wtedy stosuje się konwencjonalne procesy manualne. Odmuchiwanie sprężonym powietrzem, szlifowanie na ręcznych narzędziach pneumatycznych lub elektrycznych przy użyciu odpowiednich końcówek, frezów, tarcz ściernych.